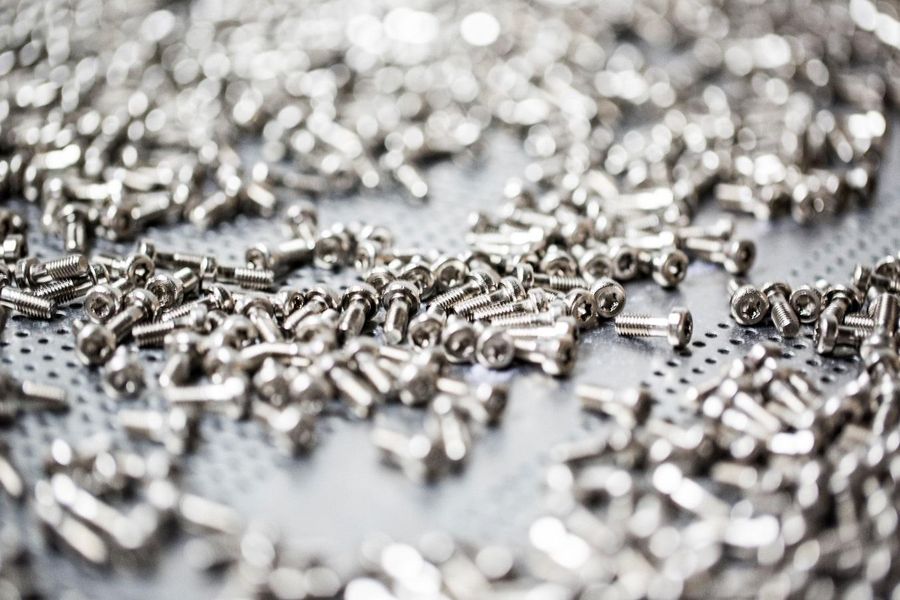
Ytbehandlingar
Stål rostar, koppar ärgar och andra metaller, utom de allra ädlaste, bryts ned på liknande sätt.
Galvanisk korrosion
Av två hopfogade metaller utsatta för galvanisk korrosion blir det den som har den lägsta potentialen som korroderas och löses upp. Den tjänstgör som anod – offeranod. Den andra metallen, katoden, blir i motsvarande mån skyddad, så att den inte korroderar. Man bör i en konstruktion alltså inte foga samman material med alltför olika elektrodpotential. I torr luft spelar det inte så stor roll, men i fuktig luft och framför allt i vatten bör man helst ha ett och samma material i en konstruktion. Ju större katodytan är desto mer syre står den i kontakt med. Och ju mindre anodytan är i förhållande till katodytan, desto mindre koncentrerad blir den galvaniska strömmen på anoden. Kombinationen liten anodyta/stor katodyta innebär därför ökad korrosionsrisk. Monteras t.ex. en liten stålskruv i en stor kopparplåt så forceras korrosionen av skruven. Omvänt gäller att en liten kopparskruv i en stor stålplåt lever längre.
Skruven ska alltid vara av ädlare material än det som sammanfogas. Helst ska det vara samma material i både skruv och det som ska fogas. När det är stor risk för galvanisk korrosion i konstruktioner med olika ädla material kan materialen isoleras elektriskt genom olika mellanlägg, lackskikt, hylsor och brickor. Hylsor och skruvsäkringar av nylon separerar metallerna, låser gängorna genom friktion, omsluter mutter och fyller ut ojämnheter. Därmed tätas förbandet mot läckage och korrosion förhindras.
Korrosivitetsklassning
Korrosivitetsklassning är en indelning av olika omgivningar, baserad på den grad av korrosion som en metall kan förväntas bli utsatta för i den specifika omgivningen. Korrosivitetsklassen är knuten till så väl miljön som metallen, eftersom olika metaller kan reagera olika på en och samma miljö. Korrosivitetsklass är egentligen endast tillämpbart på fästelement i stål, men vi har kompletterat tabellen med rostfritt stål i syfte att förbättra överskådligheten.
Korrosivitetsklasser enligt SS-EN ISO 9223 och SS-EN ISO12944-2.
Klass | korrosivitet | Exempel på miljöer | Ytbehandling / Material |
C1 | Mycket låg | Konstruktioner inomhus i varaktigt uppvärmda byggnader med låg fuktnivå och obetydliga luftföroreningar. | Elförzinkad (FZB), Obehandlad, Svartoxid, Svartförzinkad |
C2 | Låg | Inomhus vid måttlig fuktpåverkan och måttliga halter av luftföroreningar. Utomhus i luft med låga halter luftföroreningar, som inte ligger nära kust eller i tätort. | Elförzinkad 20 my (extra tjock elförzinkning) |
C3 | Måttlig | Miljöns aggressivitet: Stor. Utomhus i luft medförhöjda halter aggressiva luftföroreningar över hav eller i närheten av kust. (ej saltvatten), eller större tätorter och industriområden.Konstruktioner som är ventilerade och skyddade mot nederbörd, t.ex takstolar, vinds- och kryprumsbjälklag, konstruktioner i icke varaktigt uppvärmda ventilerade byggnader eller lokaler med icke fuktalstrande verksamhet eller lagring, tex fritidshus, kallgarage, kallförråd och ekonomibyggnader. | Varmförzinkad (FZV), Zinc Flakes (FZFL), Wirox, Geomet, Zinknickel, Zinkjärn, Atlantis Coating |
C4 | Hög | Miljöns aggressivitet: Mycket stor. Inomhus eller utomhus i industriområden med höga halter aggressiva luftföroreningar. Exempelvis vid kemisk industri, raffinaderier, svinstallar och konstglödselfabriker. Även inomhus vid ständigt mycket hög luftfuktighet eller ständig kondens. I salt ellersött vatten eller i jord exempelvis bryggor och kajer i saltvatten. | Rostfritt A2, A4, Zincotech Wirox C4 |
C5-1 | Mycket hög | Industriella miljöer. Utomhus: Kust- och offshore områden med stor mängd salt. Inomhus: Utrymmen med nästan permanent fuktkondensation och stora mängder luftföroreningar. | Rostfritt A4, Duplex |
Vanligt förekommande ytbehandlingar
Den vanligaste korrosionsskyddande ytbehandlingen av fästmaterial är elförzinkning (FZB). Zinklegeringar ger ökat korrosionsskydd och förbättrar också andra egenskaper som värmetålighet, Zinkbeläggningar har hög slitstyrka och högt motstånd mot mekanisk påverkan. Zink är en oädel metall och offrar sig till förmån för stålet. Det skyddar stålet även om skiktet är skadat. Zink korroderar under normala förhållanden ca tio gånger långsammare än stål.
Elförzinkning är en relativt enkel och billig ytbehandling. Zinkskiktet är oftast blankt men med satinzink kan också en matt aluminiumliknande yta fås. Förzinkningen ger också ett dekorativt utseende. För blankförzinkning kan ytan jämföras med en förkromad eller förnicklad yta. Vid elektrolytisk förzinkning som utförs genom elektrolys i vattenbad, beläggs 8 – 20 μm zink, beroende på önskat korrosionsskydd. Skyddsverkan är direkt kopplat till tjockleken.
Elförzinkning utförs på skruv upp till hållfasthetsklass 10.9. För högre hållfasthetsklasser är risken för väteförsprödning av materialet stor och ytbehandling utförs inte med elektrolytiska metoder. För hållfasthet över 8.8 används ett speciellt förfarande med avspänningsbehandling före ytbehandling och väteutdrivning efter ytbehandlingen.
För att ytterligare förbättra korrosionsskyddet och fördröja angreppen på zinken så det inte bildas vita fläckar (vitblemma) i fuktig atmosfär behandlas de förzinkade komponenterna med passivering, vilket har ersatt kromatering på grund av hälso- och miljöaspekter.
Zink-järnskikt ger ett betydligt ökat korrosionsskydd (ca 3 gånger bättre i saltspray) och också en förbättrad värmetålighet. Järn tillförs badet i form av en kemikalie och halten är 0,3 – 0,9 %. Beläggningen motsvarar bättre fordonsindustrins krav och kan även användas för värmeutsatta komponenter i t ex motorrum. Processen är mer komplicerad än ren zinkbeläggning och därmed också dyrare. Zink-järn behandlas med svart- eller gulpassivering.
Vår vanligaste svarta ytbehandling för stål. Färgen blir blank och flammigt svart/grå.
Zink/nickel ger ytterligare förbättring av korrosionsskyddet, upp till dubbla tiden i saltspray jämfört med zink/järn. Nickelandelen gör beläggningen hårdare och därmed är den okänslig för ytskador och tål upp till 300 °C.
Processen ger mycket liten risk för väteförsprödning men är betydligt mer komplex och därmed dyrare än zink-järn. Nickelandelen är 12 – 15 % och då bildas en stabil legering i skiktet som blir hårdare och okänsligt för skador. Skiktet motverkar galvanisk korrosion i kontakt med rostfritt och aluminium. Det kan också efterbehandlas med transparent (grå/blå) eller svart passivering. Slutfinishen är flammigt gråsvart med hög glans, ofta är den svarta färgen mer urvattnad än vid Zink/Järn behandling.
Om tjockare skikt och kraftigare korrosionsskydd krävs kan varmförzinkning användas. Det används oftast i utomhusmiljöer eller krävande inomhusmiljöer och ger ett långvarigt korrosionsskydd till ett relativt lågt pris. Vid varmförzinkning doppas komponenterna i zink vid ca 540 °C som ger en beläggning. dopptiden är beroende av detaljernas storlek och ligger mellan 1 och 3 minuter. Fästelement varmförzinkas oftast i trumma och genom att centrifugera bort överflödigt zink fås ett jämnt skikt som ofta är ca 60 μm tjockt. Skruv och mutter måste underskäras före ytbehandling med varmförzinkning på grund av att man lägger på så tjockt skikt. Exempel på skruvmaterial som ej bör varmförzinkas:
Skruv med kryssspår, insexskruv, Torxgrepp och sätthärdade material pga ythårdhet.
Varmförzinkad skruv i hållfasthetsklass 8.8 finns som lagervara och 10.9 kan beställas. Högre hållfastheter bör inte varmförzinkas på grund av anlöpningseffekter och risk för zinksprödhet, vilket innebär minskad hållfasthet och att stålet förlorar sin seghet. Zinksprödhet innebär att zink tränger in i korngränser i basmetallen vilket ger upphov till mikrosprickor. Detta kan i likhet med väteförsprödning försvaga stålet katastrofalt.
Förr gick gränsen för vilka dimensioner som kan varmförzinkas utan att toleranserna förstörs vid M10 men i moderna anläggningar kan så klena gängor som M6 i vissa fall varmförzinkas. Skikten är då tunnare, ca 40 μm.
Geomet® – GEOMET® är en icke-elektrolytiskt pålagd zinkflakebeläggning som används som korrosionsskydd på föremål gjorda av stål och gjutjärn. Geomet är den enda Zinkflake-metoden som är vattenbaserad. En unik process för optimal friktionskontroll och korrosionsskydd.
GEOMET® består av zink- och aluminiumflagor i ett oorganiskt bindemedel och är en kromfri beläggning helt fri från tungmetaller. Beläggningen innehåller smörjmedlet PTFE genom hela beläggningen. Detta ger en kontrollerad friktionskoefficient. GEOMET® finns i två vanliga tjocklekar på ytbehandlingen:
GEOMET® 500 A 5 – 8 µm – Tål 720 tim i salttest enligt ISO 9227
GEOMET® 500 B 8 – 10 µm – Tål 1000 tim i salttest enligt ISO 9227
GEOMET® 321A 6 µm – Tål 720 tim i salttest enligt ISO 9227
GEOMET® 321B 9 µm – Tål 1000 tim i salttest enligt ISO 9227
GEOMET® 321C 15 µm – Tål 2000 tim i salttest enligt ISO 9227
Användningsområden och egenskaper
GEOMET® har en silvergrå alternativt svart fin yta och kan användas inom de flesta områden för skydd av stål och gjutjärn, genom rätt valda appliceringsmetoder. Produkten är särskilt lämplig för fästelement med sin tunna beläggning.
- GEOMET® kan användas även på härdade och höghållfasta skruvar över 10.9 kvalitet
- Ytbehandlingen har begränsad ledningsförmåga och går att övermåla med de flesta organiska färger.
- Motståndskraft mot vätskor i bilar: GEOMET® har testats enligt VDA 621 – 412 och har tillfredsställande motståndskraft mot standardiserat testbränsle, diesel, motorolja, organiska lösningsmedel, kylvätska och bromsvätska. Beläggningen klarar även en nedsänkning under 24 timmar i bromsvätska med temperaturen 80° C.
- GEOMET® behåller sina mekaniska egenskaper upp till ca 300° C.
GEOMET uppfyller kraven i den europeiska återvinningslagstiftningen, i synnerhet direktiven 2000/53/EG och 2202/95/EG. GEOMET®
Geomet® 321 är en patenterad och oorganisk teknologi som består av passiviserad zink och aluminiumflingor som används för att binda ihop materialen. Denna ytbehandling är helt vattenbaserad och fri från krom och Nonylfenol gifter som gör den helt PFAS fri.
Den har en aluminiumgrå färg och är ett rostskydd för obehandlat stål. Skillnaden mellan Geomet® 500 och Geomet® 321 är smörjningen i blandningen som hjälper till med friktionen.
För att lösa problemet med smörjningen så lägger man på ett topcoat lager på Geomet® 321 så blir den likvärdig en Geomet® 500. Då heter topcoaten eller smörjningen PLUS®M som hjälper till med friktionen på skruven. PLUS®M en genomskinlig till utseendet och appliceras på samma sätt som Geometen.
Den klarar temperaturer upp till 400°c och övermålningsbara med flera lager och tål industrimedel och automobil vätskor.
PLUS®M 1 – 3 µm och är friktionskoefficient (COF) 0.12-0.18 (ISO 16047)
Svartoxid är en ytbehandling som huvudsakligen görs av utseendeskäl. Den har sämre rostskydd än vanlig FZB. Ofta ökas dock skyddet genom en efterföljande inoljning eller lackering.
Svartoxidering är en kemisk ytomvandling där stål kokas i starkt alkaliska bad varvid en svart beläggning bildas. Denna beläggning ger ett måttligt korrosionsskydd utan att påverka stålets mekaniska egenskaper. Skikttjocklek mellan 0,6-1,2 μm. Färgen blir mattsvart.
Delta-Seal har utvecklats som toppbeläggning i samband med Delta-Protect. Delta-Seal är mycket lämplig som kraftigt friktionshämmande ytbehandling av rost- och syrafasta stålämnen, som skydd mot galvanisk frätning mellan t ex rostfritt stål och aluminium. DELTA SEAL är fri från tungmetaller. Tack vare den låga härdningstemperaturen – ca 200°C, påverkas inte metalldelarnas egenskaper.
Delta-seal ger normalt skikttjocklekar på mellan 5μm och 8μm. Dess främsta egenskaper är:
- Enastående vidhäftning.
- Inga tungmetaller och god måtståndskraft mot galvanisk koorrosion
- Hög hårdhet i förening med stor flexibilitet.
- Mycket låga friktionsvärden.
- Elektrisk isoleringseffekt.
- Utmärkt kemisk motståndskraft.
Till skillnad mot de flesta andra ytbehandlingar är man vid vaxning primärt inte ute efter rostskyddande egenskaper. Vax är en billig och mycket bra friktionshämmande ytbehandling för rostfria och syrafasta produkter som förhindrar att skruv och mutter skär ihop vid montage. I ett skruvförband är det tillräckligt att bara ena delen av förbandet är belagd med vax för att avhjälpa ihopskärning. Därför är många rostfria och syrafasta muttrar förbehandlade med vax ifrån fabrik.
Består däremot förbandet av en skruv samt ett (gängat) hål i ett ämne, måste något typ av smörjmedel användas för att förhindra ihopskärning. Förbehandling med vax är då en billigt och rationell metod för att applicera ett friktionshämmande smörjmedel innan montering. Vi använder oss av Gleitmo 615 som är ett vax speciellt framtaget för gängpressande och rostfria skruvar.
Fosfatering är en kemisk process där detaljerna doppas i ett fosfateringsbad som håller 60°C -70°C under 10 – 20 minuter. Beroende på fosfateringsbadets sammansättning bildas det kristaller av zink- eller manganfosfat. Zinkfosfat i tunna skikt och med små kristaller är en förutsättning för att få bra friktionsvärden. Tjocka skikt med stora kristaller ger en våldsam spridning i friktion och därmed en likaledes varierande klämkraft. Mängden fosfat som produkterna erhåller uttrycks vanligen som en skiktvikt i g/m2. En normal skiktvikt är 12 – 25 g/m2 och motsvarar en skikttjocklek på 4 – 8μm. Korrosionsskyddet för en fosfaterad och anoljad produkt är mycket begränsad. I utomhusmiljöer uppträder rödrost i allmänhet på kortare tid än ett år.
Genom fosfatering erhålles: ett utmärkt underlag för målning – vidhäftningen mellan färgfilmen och metallytan ökar avsevärt och vid skador i färgskiktet motverkas underkorrosion. Tillsammans med inoljning ger fosfatering gott skydd mot korrosion speciellt lämpligt för massartiklar såsom skruv, bult etc. Stål och gjutjärn skyddas dock inte tillfredsställande mot korrosion enbart genom fosfatering. Zinkfosfatering är den vanligaste processen. Skikten blir grå och får en jämn yta, som efter lackering ger ett utmärkt skydd mot korrosion.